The Atmosfär chamber, which Ascott first launched in 2013, has now received an addition to its humidity control and measurement system, featuring precision psychrometric technology. We call this new system PSY-MAC for short.
Summary Features & Benefits
A solution developed in conjunction with Volvo as an approved test mechanism for the Volvo VCS 1027, 1449 (ACT-2) standard.
The addition of the PSY-MAC system provides the Atmosfär test chamber with a wider operating envelope, with improved performance at humidity levels around 95%RH.
Psychrometric humidity measurement delivers a mechanism unaffected by frequent cycles of extreme humidity, ensuring lifetime integrity of measurement.
Following the successful conclusion of trials, Ascott is pleased to announce that they are adding the PSY-MAC system to all Atmosfär test chambers supplied from September 2015.
This additional feature has been made available at no extra cost to new customers.
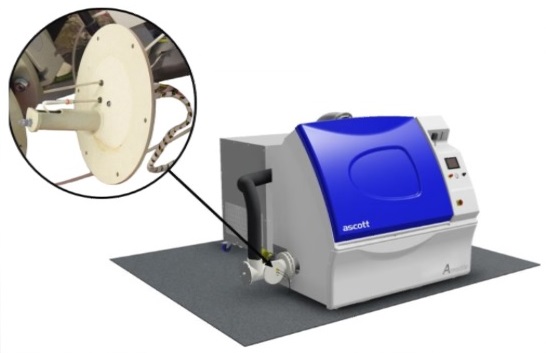
Background
The highly demanding Volvo Std-423-0014 (ACT-1, Volvo VCS 1027, 1449 (ACT-2) and Ford CETP 00.00-L-467 cyclic corrosion test standards require extended periods of climate control at 95%RH with a total calibration accuracy of +/-3%RH.
Volvo engineers in particular are convinced that psychrometric humidity measurement provides significant performance advantages over other humidity measurement techniques, especially at such high levels of humidity. Volvo engineers have indicated that it is highly likely that psychrometric humidity measurement will become mandatory within the next revision of their test standard. Therefore they requested that Ascott develop such a system within the Atmosfär chamber.
What is Psychrometric Humidity Measurement?
Psychrometric humidity measurement is a well established method for determining humidity levels in a moving air-stream. It utilises two closely matched temperatures sensors, one with the sensing element exposed (called the ‘dry’ sensor/bulb) and one with the sensing element enclosed in a ‘wet sock’ (called the ‘wet’ sensor/bulb). For anything less than a saturated (100%RH) environment, there will be a small difference in the temperature measured by these two sensors. The ‘wet’ sensor will be at a slightly lower temperature than the ‘dry’ sensor due to evaporation from the wet sock surrounding it passing into the air-stream. This difference is called the depression temperature and can used to calculated the humidity of the passing air-stream.
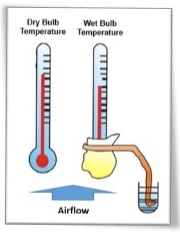
Why Add Psychrometric Humidity Measurement?
In a conventional corrosion test chamber, the use of psychrometric humidity measurement system is not viable because two of the principles requirements for accurate measurements can not be satisfied:
There is insufficient air-flow across the wet and dry sensors (this is recommend to be no less than 10m/sec).
The wet sock requires a pure water supply and will be contaminated by the pollutents (eg; salt) which are introduced into most corrosion tests and some point.
Although other humidity measurement systems, such as the capacititive sensors fitted as standard to Ascott Atmosfär chambers work well, they can only provide intermittent measurement of humidity at the 95%RH level, at the accuracy required by the Volvo & Ford tests.
The Ascott Solution
To alleviate the effects of contamination inside the chamber, Ascott’s development team came up with an innovative solution. The psychrometric humidity measurement system was placed in a module outside the chamber, between the air conditioning unit and the cabinet, isolated from the effect of the cabinets harsh environment by a large and automatically operating butterfly valve.
The required airflow of 10 m/s is provided by the ACC29 air conditioning unit and when the airflow is cut off during any cycle in the programme, valves operate to isolate the chamber from the air inlet pipe to ensure contamination cannot feed into the enclosure.
Pure water is vital for the operation of the ‘wet sock’ sensor. To provide this a header tank maintains water in the reservoir, continually overflowing to a permanent drain to ensure water purity is maintained and contamination of the ‘wet sock’ is avoided. In addition to the permanent drain, the system has a full purge at the end of every cycle to make sure the water is clean.
Extended range of humidity control
Not only is the new Ascott solution suitable for testing to the Volvo standard, it also improves the performance envelope of the Atmosfär chamber, allowing tests to be conducted in conditions to be created over a wider range of tempertature and humidity combinations.
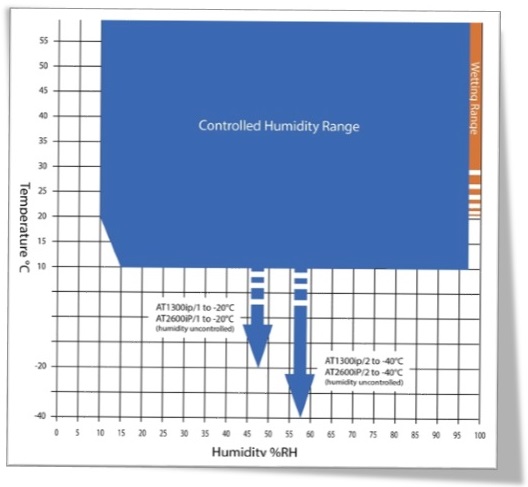