Introduction
In January 2019 Ford released a new Global Laboratory Accelerated Cyclic Corrosion Test Standard, the TM 00.00-L-467. It is quite often assumed this new standard replaced the existing Ford CETP 00.00-L-467 which was first released in October 2008, but this isn’t the case, they are similar but different standards, and here we will discuss the subtle differences.
Application
The objective of these tests is to allow evaluation of the corrosion resistance of metals in environments where there is a significant influence of sodium chloride, such as de-icing roads in winter. They are controlled tests, which can be performed anywhere throughout the world to qualify Ford components. All that is needed is a suitable test chamber, capable of complying with the requirements of each test standard.
The tests can be used as a design verification method in order to:
- Develop and qualify new corrosion resistant products,
- Develop new pre-treatments and finishing processes,
- Select materials and,
- Perform quality control of the final product.
General Requirements
Both tests are designed to be run in a laboratory environment, in a fully automatic corrosion test chamber with temperature, humidity equipped with:
- A climatisation unit to regulate the heating and cooling the temperature and controlling the humidification with a high degree of repeatability and reproducibility
- An internal circulation system for the conditioned air
- An integrated overhead swaying spray bar with a 1m clearance from the test samples (automated testing)
Both the Ford CEPT.00.00-L-467 & Ford TM.00.00-L-467 tests consists of a 7 day test profile which comprises of a 5 weekday repeating cycle. followed by a 2 day weekend phase.
The 5 day repeating cycle is made up of the following steps
- A 6 hour wet phase at room temperature, with intermittent exposure to salt spray solution (0.5%NaCl)
- A 2.5 hour transition phase with drying under climate control, this itself is performed in two parts, the first being a 30 minute ramp to increase temperature from 25°C to 40°C whilst maintaining a high humidity of 95%RH. The second part requires a 2 hour transition increasing temperature from 40°C to 50°C whilst simultaneously reducing humidity from 95%RH to 70%RH. These set values are the target conditions at the end of each phase.
- A 15.5 hour phase with constant temperature and humidity (50°C/70%RH).
The 2 day weekend phase is as follows;
- 48 hours at constant temperature and humidity (50°C/70%RH)
Specific Differences
- The Ford CEPT.00.00-L-467 test gives tolerances for the 25°C (+/-2°C) for the wetting phase at 95%RH, these tolerances have been removed in the TM Standard
FORD TM.00.00-L467 – 7 Day Profile
FORD CEPT.00.00-L467 – 7 Day Profile
2. The CEPT test states that the actual mean value of the constant temperature and relative humidity phase @ 50°C & 70%RH must be within of +/-0.4°C and +/-2%RH. This has been relaxed somewhat in the TM standard with the actual mean value allowance of +/-2C & +/-5%RH
3. The maximum allowed short-term fluctuations in temperature on the calibrated mean value is for the CEPT standard is +/-0.6°C , in the TM standard this has been relaxed to +/-1°C
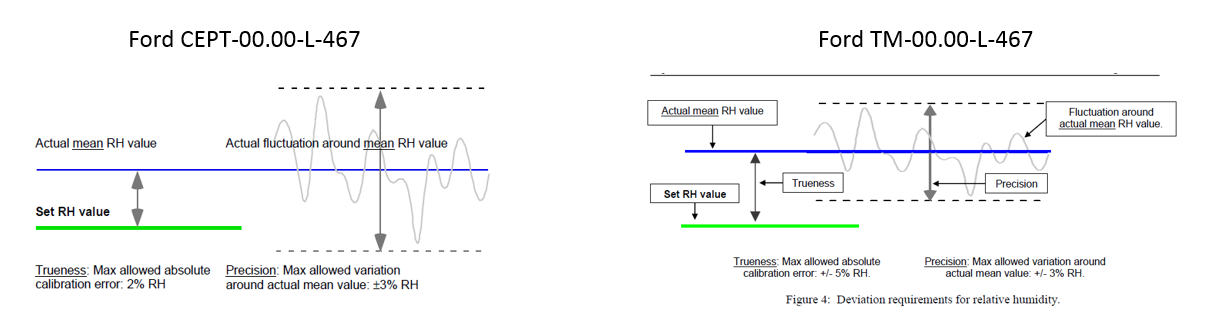
4. Two rows of vertical spray down collection beakers have been added to the TM standard, compared to the CEPT standard. This is equivalent to an extra 20 beakers used to verify the uniformity of vertical spray down is between 3 L/m² and 15 L/m² on average, throughout the 6 hour salt spraying period.
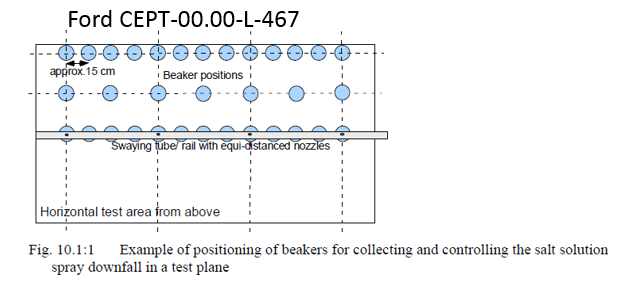
5. In the CEPT it states “Wall heating should be avoided, due to that heating by radiation tends to keep test object close to the chamber walls locally too dry to be within humidity specification (or a screen shall be installed to avoid such an effect).”
In the TM Standard it states “Wall heating must be avoided since heating by radiation tends to keep test objects that’s are close to the chamber walls too dry to be within the humidity specification”
This is a very subtle but important difference to the standards as it changes the way manufacturers of compliant chambers generate heat during high humidity modes of operation
6. Test panel angles in CEPT are allowed to be within 15-20° from vertical, in the TM this is 20° +/-5 degree from vertical.
Specific Additions
Now we have discussed the various differences, let’s turn our attention to the additions in the Ford TM standard which are not stated in the CEPT.
- The submitted temperature and humidity profile must come from an independent data logger, the Vaisala HM141 in particular is recommended. The CEPT standard does not recommend any particular type of logger.
- A whole new section on target gauge loss figures of 150-250 micron has been added to the Ford TM standard. Measurements taken in accordance with either FLTA CA 005-01 (using a Starrett 760FL Screw Thread Micrometer) or FLTA CA 006-01 (using an Olympus 38DL Ultrasonic Thickness Gauge). The gauge loss is to be verified every quarter by using a minimum of 3 ACT Test panels (Part ref: 61934), the submitted profile data for verification should also come from an independent monitoring device positioned amongst the test samples in the test plane.
Here is an example approved by Ford Corrosion Engineering dept. of the 6 week gauge loss required by Ford TM Spec recorded in an Ascott AT1300IPLite chamber
Test results collected in an AT1300IPLite from Ascott Analytical:
Summary
Both these tests are subtly different. One does not supersede the other and both tests can be run using an Atmosfär Chamber manufactured by Ascott.
The test methodologies for either standard can be downloaded by clicking the following links:
Ford CEPT 00.00-L-467 Test Methodology – Click here
Ford TM 00.00-L-467 Test Methodology – Click here
For further information on these test standards or any other standards, please get in touch and see how we can help you.
Contact us via email on sales@ascott-analytical.com
Alternatively call us on +44 (0) 1827 318040
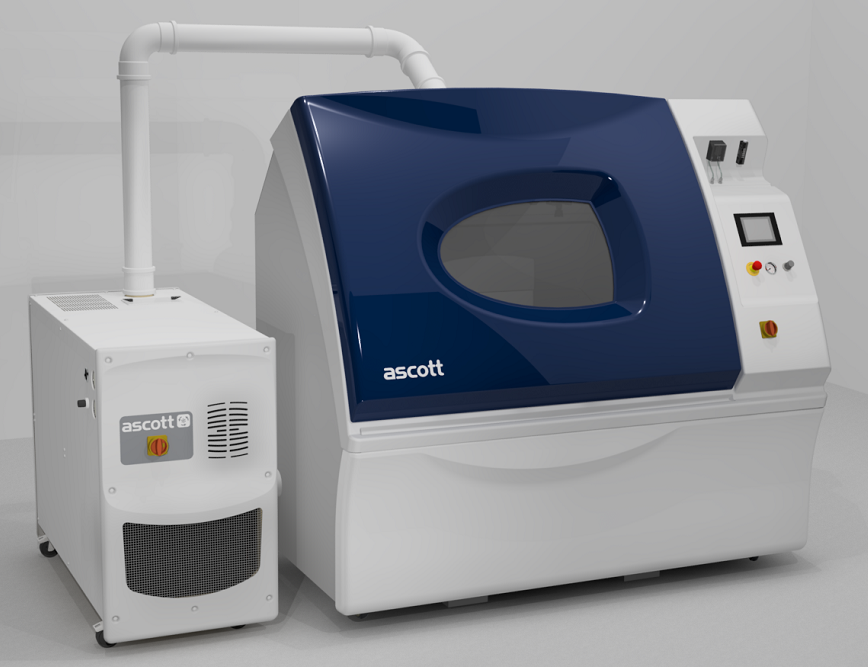